Wireless That Works
Experience driven wireless monitoring
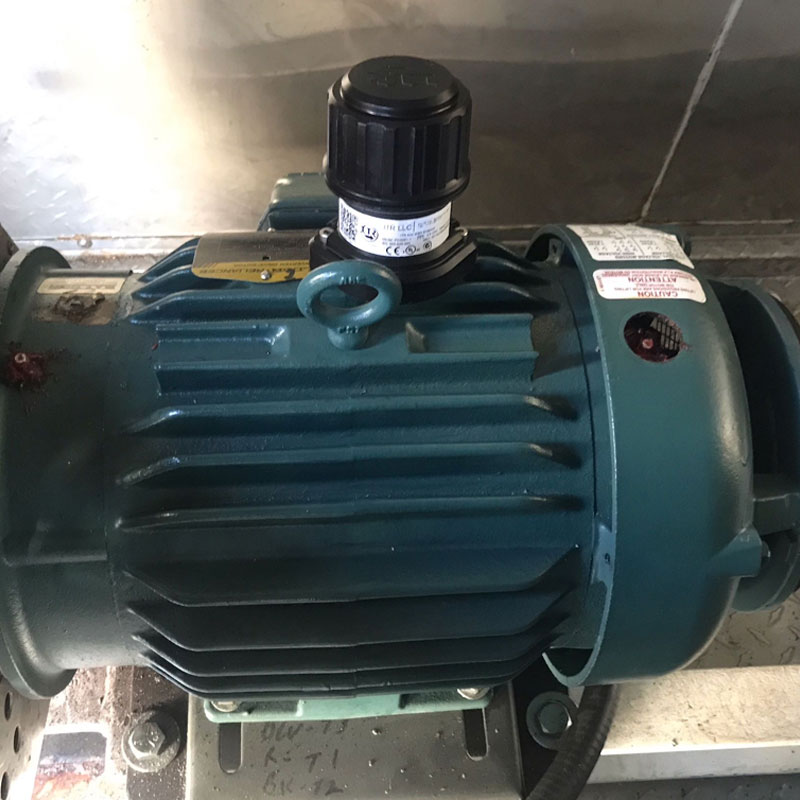
Wireless Monitoring
In the landscape of modern industrial operations, the integration of wireless monitoring represents a evolutionary step towards more efficient and effective predictive maintenance strategies.
When integrated into fully hybrid toolbox of predictive maintenance solutions, wireless monitoring offers unique advantages in capturing real-time data from diverse equipment and processes across the industrial spectrum through proactive asset management. The real-time data obtained through both wireless and hard wired sensors facilitates predictive analytics, allowing for the early detection of anomalies and potential equipment failures.
Moreover, the synergy between wireless monitoring and other predictive maintenance tools, such as vibration analysis, thermography, or predictive analytics software, creates a robust ecosystem. This hybrid approach amalgamates diverse data sources and predictive models, enabling a holistic view of asset health. It empowers maintenance teams to make data-driven decisions, identify trends, and refine predictive algorithms, thereby enhancing the accuracy and effectiveness of maintenance strategies. which leads to significantly reducing unplanned downtime, optimizing maintenance schedules, and prolonging asset lifespans.
The ITR Approach
Actionable Analysis Requires Experience
In the rapidly evolving realm of industrial operations, the role of experienced data analysis stands as a critical linchpin in driving the transformative power of Predictive Maintenance (PdM).
Experienced data analysis in PdM is pivotal for today’s industrial environments as it enables proactive identification of equipment anomalies and potential failures. By employing advanced algorithms and machine learning techniques, analysts can scrutinize years of historical data, sensor readings, and operational parameters from a comprehensive toolbox of readily available and synchronized data sources to predict when machinery might deviate from optimal performance. This foresight allows for planned interventions, minimizing unexpected downtimes, reducing costly repairs, and optimizing overall equipment reliability.
Furthermore, in complex industrial ecosystems, data analysts proficiently navigate through massive datasets to derive actionable insights. Their ability to communicate these findings effectively to maintenance teams and decision-makers empowers organizations to make data-driven decisions. This fosters a cohesive approach towards optimizing maintenance schedules, resource allocation, and operational strategies, thus propelling the industrial environment towards continuous improvement and operational excellence.
Ultimately, the value of experienced data analysis in Predictive Maintenance cannot be overstated. It serves as the bedrock for minimizing downtime, optimizing resource utilization, reducing operational costs, and ensuring the longevity of critical assets. By embracing data-driven approaches, companies can propel themselves towards sustainable growth, competitiveness, and resilience in today’s ever-evolving industrial landscape.
The Details
830 Wireless sensor network (WSN)
The ITR 830 WSN is a wireless, battery powered solution for tracking real time temperature and vibration on industrial equipment and providing early warnings for potential failure modes. The system is comprised of an Endpoint sensor assembly, a Coordinator, and a Repeater. All installations require at least one Endpoint and one Coordinator, but a broad wireless sensor network can be configured using Repeaters to encompass an entire industrial complex.
Why Partner With ITR
Our Approach
Experience
Experience is an indispensable consideration when it comes to choosing a PdM Provider. While price and “ease of entry” might seem like a winning combination initially, without exception, investing in experience reaps inimitable, long-term rewards.
Four decades of accumulated analytics data, in the hands of ITR’s seasoned analysts, each of whom brings years of hands-on knowledge, deliver fine-tuned strategies and a proven track record of PdM saves and solutions.
Expertise
Integrated in-house expertise: certified analysts, design engineers, software developers, and data scientists working as an integrated team for both daily customer support and ongoing, long-term R&D
Integration
Seamless integrated with ITR’s best in class 5-channel portable data collection unit (DCU) for advanced follow up studies.
Ease and simplicity of implementation and use.
Reinvestment
More than 20% of our revenue is reinvested in systems and services that directly benefit our customers with active subscriptions. This significant commitment to the future of PdM showcases our dedication to providing the best possible outcome for our partners trust in ITR.